Сварочное оборудование
/Сварочные швы: виды и способы сварных соединений
Сварочные швы: виды и способы сварных соединений
20.11.2023
Что такое сварочное соединение?
Процесс, сопровождающийся нагревом двух деталей, их плавлением и пластической деформацией, в результате которых образуются общие атомные связи. Это один из самых эффективных и универсальных способов создания разъемных соединений металлических заготовок. Для одних и тех же целей может использоваться несколько способов:
Процесс, сопровождающийся нагревом двух деталей, их плавлением и пластической деформацией, в результате которых образуются общие атомные связи. Это один из самых эффективных и универсальных способов создания разъемных соединений металлических заготовок. Для одних и тех же целей может использоваться несколько способов:
- Пайка широко применяется в радио- и электромашиностроении.
- Клей подходит для получения слабонагруженных деталей, а также сборки изделий из разнородных материалов.
- При этом наиболее прочные неразъемные соединения можно сделать при помощи сварочного, а также заклепочного оборудования.
В последнем случае используются специальные детали, которые вставляются в заранее просверленные отверстия. После этого производится осадка замыкающих головок. Заклепочное соединение по своему удобству, прочности, технологичности значительно уступает сварному. Процесс многоэтапный, дорогой, сложный и трудоемкий.
Поэтому сварка является основным способом соединения в машиностроении, строительстве, судостроении, химической и военной промышленности и многих других отраслях. Данный метод позволяет работать с разными металлами, деталями почти любой формы и размера. Сварочное (или сварное) соединение образует 4 зоны, где есть: шов, место стыковки (сплавления), участки нагрева и прилегающие части, не подвергающиеся термическому воздействию. Использование современного сварочного оборудования позволяет:
- удешевить изготовление, повысив производительность;
- частично или полностью автоматизировать процессы;
- обеспечить герметичность без задействования других процессов;
- создать шов с заданными характеристиками.
Среди недостатков сварного соединения стоит отметить возможность разрушения под воздействием высоких вибрационных нагрузок. Детали, работающие в такой среде, чаще всего соединяются заклепками. В остальных случаях технология сварки лучше, прочнее и надежнее других. Главное – правильно подобрать оборудование и следить за качеством получаемых швов.
Виды сварочных швов
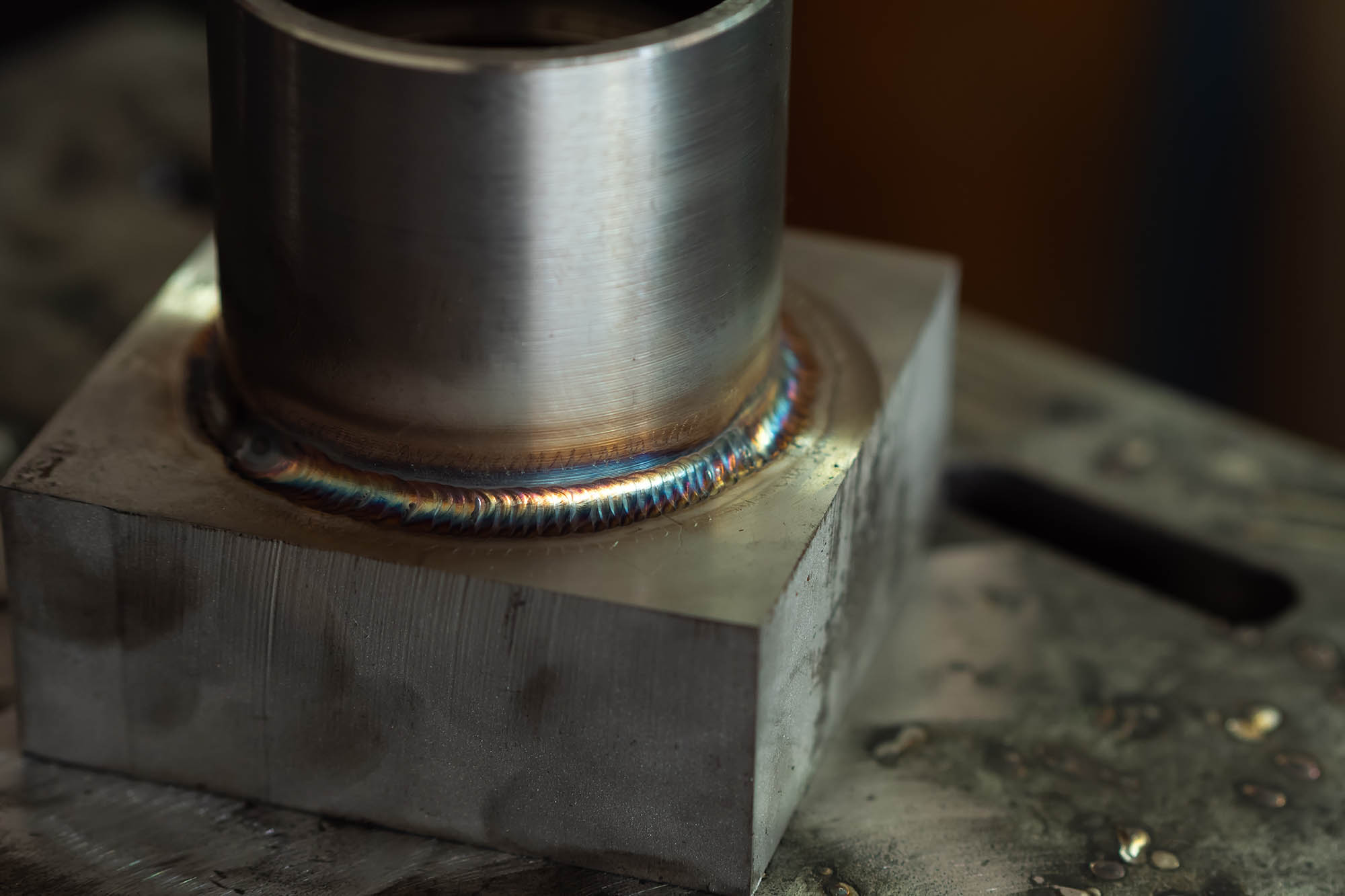
Связующая зона, как правило, образуется вследствие плавления сварочной ванны и последующей её кристаллизации (после остывания). В контактном способе соединение деталей формирует диффузия. В обоих случаях от качества, ширины, глубины, формы (и некоторых других характеристик) сварного шва зависят прочность соединения и внешний вид. Как именно можно соединять детали?
- Прямые швы. Используются для сварки деталей одной линией. Могут выполняться как одним плавным движением, так и рисунком (например, зигзагом). Чаще всего используются для стыкового соединения, предполагая проведения работ с одной или двух сторон. В зависимости от толщины заготовок, кромки могут быть загнуты вверх (очень тонкие листы), сточены (или срезаны) в форме V, X или U (для толстых деталей ответственного назначения).
Прямые швы – наиболее простые в реализации. Именно с них начинается практическое обучение начинающих сварщиков. Уровень сложности задает пространственное положение. Ровные, качественные горизонтальные и потолочные швы – признак большого мастерства. Ведь данный тип работ требует особой сноровки и техники. Даже в полугоризонтальном положении расплавленный металл будет стремиться спускаться вниз. Чтобы этого не происходило, используется особый рисунок – схема движения электрода в сварочной ванне, например, в форме спирали.
- Угловые швы. Используются для соединения двух деталей, расположенных друг к другу под острым, прямым или тупым углом. Такая работа может производиться с внешней или внутренней стороны, от чего будет зависеть техника наложения сварного валика. В обоих случаях особое внимание уделяется провару корня. Если речь идет о соединении двух толстых заготовок снаружи, то сварка выполняется в три подхода. Сначала прямым движением формируется коренной шов. Далее кольцевыми движениями накладывается валик на нижнюю часть, затем на верхнюю. Тонкие и средние заготовки можно соединить в один либо два этапа. В последнем случае после формирования корневого шва следует общая широкая проварка.
Создание неразрывного соединения с внутренней стороны актуальна для деталей, расположенных под прямым или тупым углом. В этом случае шов можно сформировать за один раз (по аналогии с тавровым соединением). Хорошим решением будет выбор сложного рисунка, где после движения электрода из стороны в сторону он продвигается дальше (вдоль стыка) для провара корня. Тренировать данную технику нужно с нижнего положения, постепенно увеличивая сложность изменением оси сварки. Горизонтальные, вертикальные, потолочные и их вариации угловых швов (полугоризонтальные, полупотолочные и т.д.) помимо всего прочего требуют контроля над текучестью металла.
- Тавровые швы. Используются для создания деталей Т-образной формы с односторонней, либо двухсторонней фиксацией. Заготовки толщиной 2 и более см требуют снятия фаски для хорошего провара (с торца привариваемой детали). Технология аналогична созданию угловых неразъемных соединений, предполагая заполнение внутреннего угла сварочным валиком. Её высокая распространенность стала причиной внесения правил сразу в несколько ГОСТ, среди которых: ГОСТ 5264 80 (для ММА), ГОСТ 14806-80 (для соединений без предварительной подготовки кромок), ГОСТ 14771-76 (для сварки в среде защитных газов).
Тавровый шов подходит для работы с деталями разной толщины, а также монтажа в труднодоступных местах. С его помощью крепят балки, монтируют ограждения, усиливают существующие металлоконструкции. Как и другие виды соединений, тавровое может выполняться разными техниками, отталкиваясь от объема заполнения, вида сварочного оборудования и требований проектной документации.
- Кольцевые швы. Данный термин используется в двух случаях. 1 – во время создания замкнутого шва, например, для приваривания детали цилиндрической формы к плоскому основанию. Кольцевым швом также можно назвать стыковое соединение трубопровода. Сложность заключается в изменении пространственного положения, которая требует от мастера смены рисунка (например, с елочки на полумесяц). 2 – во время наложения сварочного валика круговыми (кольцевыми) движениями, повышая прочность фиксации и глубину провара.
Сложность работы с кольцевыми стыками заключается в неравномерном напряжении, которое можно уравновесить разными способами. Например, во время наложения нескольких слоев нужно менять их направление и смещать точки стыков. Сегментированная сварка крест на крест используется для стыкового соединения труб большого диаметра. Для повышения качества работ (в производственных условиях) рабочее место может оборудоваться вращательным механизмом.
Основные характеристики сварочных швов
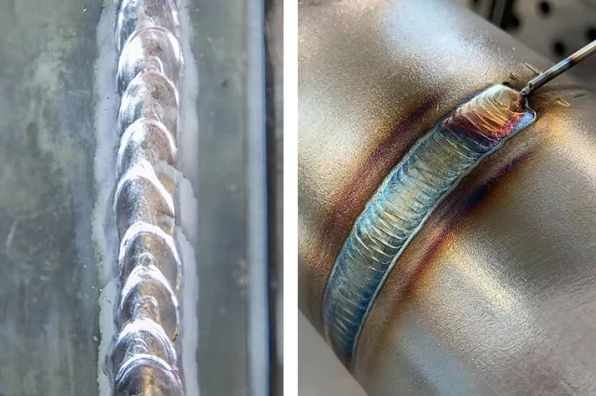
В зависимости от положения деталей по отношению друг к другу, швы могут затрагивать одну (стыковые соединения) или несколько плоскостей. В первую группу стоит отнести и торцевую сварку. В этом случае детали плотно прилегают друг другу. Общий шов объединяет именно торцы, образуя прочное неразрывное соединение. Оно имеет высокую сопротивляемость нагрузкам, часто используется для сварки тонколистовых заготовок с целью увеличения площади провара и защиты от прожогов.
Когда шов затрагивает две и более плоскости? В создании угловых, тавровых, а также деталей, расположенных внахлест. В последнем случае валик объединяет торец одной заготовки с плоскостью другой. При этом сами детали располагаются параллельно (накладываются друг на друга). Достоинства: невысокая сложность, возможность проварки будущего изделия с двух сторон для повышения прочности. Торцевая сварка часто применяется для работы с габаритными, тяжелыми деталями. Какие еще характеристики можно выделить?
- Форма поверхности. Она может быть плоской, выпуклой или вогнутой. Выбор зависит от назначения соединения. Если оно будет подвергаться динамическим нагрузкам, то наваривается утолщение, в том числе при помощи несколько слоев. Плоская поверхность улучшает внешний вид, вогнутые швы снижают время нагрева, что часто используется для работы с тонкими деталями. Два последних варианта подходят для работы в условиях динамических нагрузок.
- Протяженность и однородность. Сварочный валик может накладываться с одной (только с внешней) или двух сторон (в том числе с внутренней). Он может быть однородным (цельным) или прерывистым. В процессе реализации последней техники снижается риск прожога за счет уменьшения тепловой нагрузки. Прерывистое или точечное двухстороннее соединение может быть зеркальным или располагаться в шахматном порядке (со смещением).
- Пространственное положение определяет сложность и технику выполнения сварки. Нижние швы – это когда детали расположены горизонтально (например, лежат на верстаке), а валик накладывается сверху. По данному критерию швы также разделяются на: вертикальные, потолочные, наклонные (полупотолочные, полувертикальные, полугоризонтальные).
- Однослойные и многослойные швы. Соединение может выполняться за один проход или несколько. Последний вариант используется для соединения толстых заготовок, а также создания рабочих швов ответственного назначения.
- Качество поверхности. Оно зависит от назначения, уровня зашлакованности, техники выполнения и типа сварки. Самыми чистыми и красивыми являются соединения, сделанные в среде защитных газов. Они не требуют механической доработки (стачивания, шлифовки), сокращая время производства.
- Структура шва. В процессе расплавления соединяемых деталей и присадочного материала образуется общая плавильная зона (или ванна). Переход из жидкого состояния в твердое сопровождается образованием микрокристаллов, которые и связывают две заготовки между собой. Форма кристаллов определяет прочностные характеристики, имея зависимость от интенсивности нагрева и охлаждения, а также состава присадочного материала. Структура шва тесно связана с рисунком, который помогает сварщику задавать те или иные характеристики. К примеру, спиральные движения электродом ММА позволяют вытеснять шлак по сторонам, при этом увеличивать глубину провара за счет наложения линий прогрева друг на друга.
Способы сварных соединений
В зависимости от того, какое оборудование, технология, материалы используются, шов получает набор характеристик и свойств. Какой бы не была высокой квалификация сварщика, она не позволит добиться от ММА инвертора такой чистоты соединения, как например, от TIG аппарата. Их выбор в том числе зависит от материала деталей, что объясняет незаменимость оборудования для проведения тех или иных работ.
- Ручная дуговая сварка (MMA, РДС, SMAW). В работе используются покрытые электроды, в которых стержень является присадочным материалом (плавится вместе с деталями), оболочка образует защитную среду (выделяя шлак). Характеристики ММА шва зависят от силы и типа тока (постоянный, переменный), диаметра и состава электрода, навыков мастера. Особенности:
- компактность оборудования – удобство сварки на объекте;
- длина непрерывного шва в один проход ограничена электродом;
- необходимость обработки зоны соединения (удаления шлака, шлифовки);
- сравнительно невысокая производительность;
- качество сильно зависит от мастерства сварщика;
- универсальность (подходит для большинства видов сталей, заготовок разной толщины) за счет широкого выбора марок и диаметров электродов.
- Полуавтоматическая сварка в среде защитных газов (MIG/MAG). Через специальную горелку в зону плавления подается проволока (присадочный материал) и защитный газ. Последний защищает сварочный процесс от негативного воздействия воздуха, в результате которого в том числе образуется шлак. Проволока (материал и толщина) выбирается, исходя из состава и параметров соединяемых металлов. Благодаря высокой доли автоматизации MIG/MAG широко используется на предприятиях. Технология подходит для соединения малоуглеродистых, низколегированных, конструкционных и других сложных (в работе) сталей. Особенности:
- ровный красивый шов за счет отсутствия примесей (оксидов, флюса, шлака) и равномерной подачи присадочного материала;
- повышенный уровень опасности (газовое оборудование + вредные испарения);
- небольшая ширина шва при высокой прочности соединения;
- для работы, помимо самого аппарата MIG/MAG, нужен баллон с газом.
- используется в основном для сварки деталей небольшой толщины;
- удобство создания швов в любом пространственном положении.
- Сварка под флюсом. Используется для соединения цветных металлов, легированных и углеродистых сплавов. Защитная среда создается флюсом - порошком или гранулами, защищающими сварочную ванну от внешнего воздействия. В процессе формирования шва повышается концентрация тепла и не образуются брызги. В том числе благодаря этому увеличивается глубина провара и скорость - металл осаждается быстрее, чем при использовании других технологий. Особенности:
- однородный шов с повышенными коррозионными свойствами (в том числе благодаря высокой стабильности горения дуги);
- невозможность работы в сложных пространственных положениях из-за сыпучести защитного материала;
- повышенный уровень безопасности для сварщика;
- использование дорогостоящего сложного оборудования;
- подходит для формирования шва в ручном и автоматическом режимах;
- неровные края детали, требующие дополнительной механической обработки.
- Электронно-лучевая и лазерная сварка. Используется для соединения тугоплавких металлов, разнородных материалов, сплавов, обладающих высокой химической активностью. Отличается высокой концентрацией теплового воздействия при минимальном диаметре лучевого пятна. Данный способ позволяет создавать швы небольшой ширины даже при работе с толстыми заготовками. Уменьшение зоны теплового воздействия защищает прилегающие участки от деформации. Особенности:
- повышенная точность – подходит для изготовления измерительного и другого оборудования;
- малый объем расплавленного металла;
- более прочная кристаллическая решетка в зоне шва;
- бесконтактный способ и высокая скорость работ.
Влияние материала на выбор способа сварки и типа шва
Металлы обладают разными свойствами, которые определяют условия, создаваемые для их соединения. Поэтому на выбор сварки в первую очередь влияет состав: объем углерода, количество вредных примесей, свойства и виды легирующих добавок. Если неразъемное соединение можно создать разными способами (например, газовой, полуавтоматической и ручной дуговой сваркой), то выбор определяют:
- назначение детали с учетом будущих нагрузок и условий эксплуатации;
- финансовые и временные затраты – выбирается вид сварки, способный повысить производительность и снизить цену;
- характеристики шва (чистота, протяженность, положение в пространстве, его размеры, форма и т.д.).
Для соединения активных металлов, например, деталей из алюминия, требуется создание зоны защиты инертными газами. Данный метод подходит и для работы с другими сталями, однако не имеет финансовой целесообразности. В этом случае лучше выбрать ручную сварку плавящимися электродами. Другой пример. Наибольшей производительностью (в диапазоне толщин 5-20 мм) обладает сварка под флюсом. При этом она не очень хорошо подходит для работы с металлами, обладающими высокой теплопроводностью (уступает электронно-лучевой), как и создания швов в разных пространственных положениях (стоит выбрать TIG оборудование).
Ошибки и дефекты сварочных швов
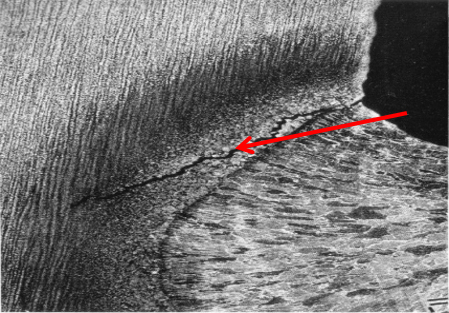
Соединения металлов, создаваемые под влиянием высоких температур, могут иметь различные недостатки. К дефектам относят изъяны сварочного шва, появившиеся вследствие неверной настройки оборудования, неправильного выбора технологии или материалов. Их наличие снижает прочность конструкции, сокращает срок службы, ухудшает внешний вид. Все дефекты можно разделить на три группы:
- Внешние (определяемые на глаз). Смещение кромок, наплывы (утолщения), кратеры (ямки, углубления), трещины (физическая неоднородность), подрезы (канавки) и другие поверхностные недостатки сварного шва.
- Сквозные. Опасные с точки зрения снижения нагрузочной способности дефекты, нарушающие физическую целостность зоны сварки. Наличие сквозных щелей, трещин и прожогов является признаком брака детали.
- Внутренние (структурные). Изъяны, связанные с неправильным или неполным сплавлением заготовок, в результате чего сварочный шов не получает нужную прочность и однородность. К таким можно отнести повышенную пористость, непровары и загрязнения (присутствие посторонних веществ).
В большинстве случаев дефекты являются следствием неправильного выполнения сварочных работ. Поэтому начинающим мастерам важно знать причины их появления и учиться устранять собственные ошибки на практике.
- Трещины разделяются на горячие и холодные. Первые образуются в процессе усадки металла (особенно актуально для сталей с высоким содержанием углерода и хрома в составе), вторые являются следствием остаточного напряжения (могут появляться при быстром остывании шва).
- Наплыв – сосредоточение расплавленного металла, которое после остывания не образует прочной связи со швом. Данный дефект связан с перегревом зоны сварки, неравномерным распределением материала при помощи электрода.
- Кратер – углубление, образующееся в результате неравномерной усадки металла, а также при отключении дуги. Значительные дефекты можно устранить точечным подвариванием.
- Свищи – множественные полости (небольшого размера) в сварном валике, снижающие его прочность. Их наличие может говорить о неверной настройке оборудования, а также неправильном выборе присадочного материала.
- Непровар – внутренний участок шва, не имеющий молекулярной связи, появившийся из-за малого (или неравномерного) нагрева. Причины – малая мощность, быстрое движение электрода, большая толщина детали, например, требующая сварки с обеих сторон.
- Прожог – сквозное отверстие, вызванное подачей избыточной энергии. Данный дефект особенно часто встречается во время работы с тонколистовыми деталями.
- Пористость – структурный недостаток, являющийся следствием присутствия воздушных пузырьков в расплавленном металле. Прочность шва снижается, повышается риск появления трещин в процессе нагрузки. Причины – низкое качество электродов (или их неправильный выбор), высокая скорость сварки, попадание шлака и посторонних веществ.
Виды изъянов в сварных швах и причины их появления подробно расписаны в ГОСТ 30242-97.
Способы обнаружения и устранения дефектов
Недостатки сварного шва можно идентифицировать разными способами, самым простым из которых является визуальный осмотр. Перед началом оценки обязательно нужно очистить поверхность от шлака при помощи молотка и металлической щетки. Осмотр можно производить как с увеличительным прибором (микроскоп, лупа), так и без него. На что именно нужно смотреть? На сварочный валик, выявляя зашлакованность, трещины, свищи, кратеры. Также стоит обратить внимание на геометрические показатели, которые указываются в чертеже. Для измерения ширины, усиления (наплавления), межваликого западания (у многослойных швов), катетов угловых соединений и некоторых других характеристик можно использовать специальный инструмент – шаблон сварщика.
Визуальный способ обнаружения не подходит для выявления внутренних дефектов. Для этих целей используются разрушающие или неразрушающие методы контроля. К первой категории можно отнести:
- Высверливание отверстия для визуальной оценки зоны сварки в разрезе.
- Вырезание части детали для проведения практических испытаний. Таким способом можно проверить соединение на ударную вязкость, прочность и т.д.
К числу неразрушающих методов проверки качества сварного шва относятся:
- Проверка однородности рентгеном (для соединений глубиной до 60 мм). Присутствие на снимках темных участков будет говорить о наличие непроваров, структурных трещин, шлаковых накоплений.
- Проверка ультразвуком. С помощью специального оборудования на шов воздействуют звуковыми волнами частотой от 20 кГц. Отраженные сигналы и преобразованные в электрические импульсы выводятся на экран в виде графической модели. На последней хорошо видны все дефекты, а также – их размеры, глубина залегания, место расположения.
- Проверка магнитным полем (для швов толщиной до 12 мм). Позволяет выявить поверхностные и внутренние изъяны, которые после намагничивания детали проявляются на магнитной пленке. Данный метод часто используется для контроля над соединением деталей из цветных металлов.
Также существуют физические методы проверки непроницаемости сварных швов при помощи различных жидкостей и газов под давлением и без него. В качестве рабочей среды используется вода, воздух, вакуум, аммиак (химический способ), керосин (капиллярный метод)
Определение качества шва
Соединение должно соответствовать обозначениям в чертеже, где указывается: ГОСТ, вид сварки, длина непрерывного участка, размер катета и другие технические характеристики. Во время работы нужно следить, чтобы зона сварки не зашлаковывалась и не перегревалась, сварочный валик имел однородную структуру и одинаковые размеры.
После остывания на поверхности шва (а также в прилегающей зоне термического воздействия) не должно быть трещин, наплывов, кратеров и других внешних дефектов. Рисунок (кристаллическая решетка) должен обеспечивать прочное соединение деталей и глубокий провар. Ответственные швы проверяются одним из методов контроля с использованием профильного оборудования (радиационным, ультразвуковым и т.д.), ведь внутренние дефекты невозможно определить визуально.
FAQ
Как правильно подготовить металлические поверхности перед сваркой, чтобы обеспечить хорошее качество шва?
Зона соединения зачищается стальными щетками, абразивными кругами или пескоструйным способом, обезжиривается (растворителями, растворами кислот). С торцов заготовок и на поверхностях не должно быть влаги, ржавчины, шлака, жировых пятен. Если это предусмотрено чертежом, кромки срезаются или стачиваются для получения нужной формы.
Как избежать появления трещин в сварочном шве при работе с высокопрочными сталями?
Нужно правильно настроить силу тока, подобрать электрод (диаметр, заточка, состав) и присадочный пруток (проволоку), отталкиваясь от материала изготовления деталей и их толщины. Снизить внутреннее напряжение можно, предварительно прогрев заготовки и избавив от быстрого остывания в процессе осаждения металла в сварочной ванне.
Как провести визуальный контроль сварочных швов и что указывает на хорошее качество сварки?
Тщательно очистить шов от шлака и окалин, осмотреть зону соединения на присутствие трещин, свищей и других внешних дефектов. Для измерения параметров шва стоит использовать шаблон сварщика. Качественный шов имеет однородную кристаллическую решетку с минимальным содержанием шлака. Его рисунок должен соответствовать выбранной схеме наложения сварочного валика (без значительных отличий в форме и размерах).
Как устранить дефект "шпатов" (излишков сварочного металла) в шве при сварке методом TIG?
Правильно настроить силу тока, выбрать подходящий диаметр электрода, форму и размер газовой линзы. Много сварочного металла также может быть из-за использования присадочного прутка слишком большого диаметра.
Как оценить прочность сварочного шва и какие тесты следует провести для его проверки?
Прочность соединения снижается, если в нем присутствуют дефекты (трещины, свищи, кратеры, зашлакованность). Их можно идентифицировать методом визуального осмотра. Также существуют механический способ проверки соединения на прочность на тестовом образце. Для контроля качества шва без разрушения используется ультразвуковое и рентгеновское оборудование.
Как сварить тонкие металлические листы без искажений и деформации?
В зависимости и вида сварки, можно выбрать режим «пульс» или наложить прерывистый шов. Для защиты от деформации также можно загнуть края для увеличения общей толщины металла и выполнить торцевую сварку. Если на электрод постоянного тока направить плюсовой заряд, преимущественный нагрев получит присадочный материал (а не деталь). Также важным условием работы с тонким металлом является правильный выбор диаметра электрода и скорости его перемещения.
Как обнаружить скрытые дефекты сварочных швов с помощью неразрушающего контроля?
Для этого можно использовать один из методов – оптический, капиллярный, вихретоковый, радиоволновый, магнитный, электрический, тепловой, акустический, радиационный. Опираясь на физические свойства разных материалов, эти способы позволяют увидеть внутренние трещины, пористость, посторонние включения, непровары и другие дефекты шва.
Как правильно выполнять сварку труб, чтобы обеспечить их герметичность и прочность?
Изменение пространственного положения повышает сложность данного вида работ. Движение вверх требует подъема жидкого металла, чтобы не было наплывов. Для обеспечения герметичности соединения необходимо наложить непрерывный сварочный валик от начала до самого конца.
Какие используют методы очистки сварочных швов после завершения работы для улучшения внешнего вида и защиты от коррозии?
Для получения красивого соединения используется УШМ, с помощью которой стачивается, а затем полируется зона шва. Коррозионную стойкость придает последующая обработка сварочной химией. Специальные средства в виде пасты или спрея удаляют остатки шлака и следы окисления, создают защитную пленку, исключая контакт необработанного металла с воздухом и влагой.
Какой метод сварки наилучший для соединения алюминиевых деталей?
Алюминий – активный металл, образующий окислы при контакте с воздухом. Поэтому для чистого и прочного соединения требуется создание защитной среды. Для этих целей лучше всего подходит TIG оборудование. Если нет строгих требований к качеству, можно эту работу выполнить полуавтоматом или даже инвертором ММА (грамотно настроив силу тока и выбрав подходящий электрод).
Другие новости
- 04.10.2023 Сварка аргоном Подробнее
- 05.12.2023 Сварка алюминия Подробнее
- 06.11.2023 Сварка электродами Подробнее